There’s no denying that ceramics are stunningly beautiful objects, with intricate detailing and ornate designs that can really set the tone in any given space. Their delicate yet durable nature has been treasured for centuries, transfixing viewers with their sheer beauty and mesmerising craftsmanship. If you’re keen on dipping your toes in the pottery realm, you’ll want to take a closer look at the pottery kilns used in the firing process.
These machines are incredibly complex and multifaceted, with a range of features that can make or break your perfect ceramic piece. It doesn’t matter if you’re trying to craft the perfect serving tray for throwing unrivalled parties or a set of gorgeously glazed mugs that will make your morning cup of coffee that much more enjoyable – the success of any ceramic creation lies in the right pottery kiln.
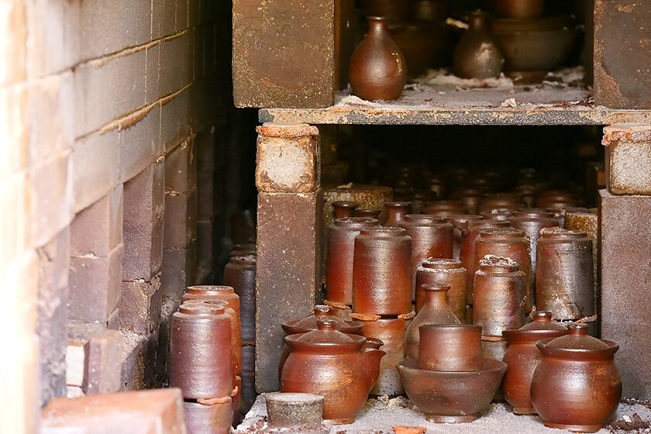
What Types of Pottery Kilns Are There?
To truly capture the beauty of your ceramic masterpiece, you’ll need to take a look at the wide range of reliable and efficient pottery kilns available on the market. They’re specifically made to withstand the immense heat and pressure required for firing, while also providing a safe atmosphere so your piece doesn’t end up in shatters.
Electric
Starting off with the most common type, electric pottery kilns are used by both hobbyists and professional ceramists alike. They rely on electricity for their power source, which makes them the most cost-effective option in terms of energy consumption. They’re directly connected to a wall outlet, so you don’t have to worry about combustible gas emissions or fumes into the atmosphere.
When the electric kiln is in use, it’ll produce a steady and consistent heat that will ensure your ceramic piece holds its shape entirely. The temperature range gradually increases or decreases with the help of a controller, allowing you to fire at certain speeds and keep your piece from cracking.
Gas
The next type involves a gas-fired pottery kiln, which is generally used in industrial settings or professional businesses. These machines rely on propane, natural gas, or butane for their power source, which means they’ll be more expensive to run than electric models. They need a consistent and powerful source of fuel to reach higher temperatures in a shorter amount of time, which inherently speeds up the entire firing process.
This results in a more intense heat that’ll burn away any unwanted particles and leave behind a clean and beautifully glazed ceramic piece. The temperature range can be easily adjusted with the turn of a few knobs and dials, so you can get to the proper heat level that suits your pieces.
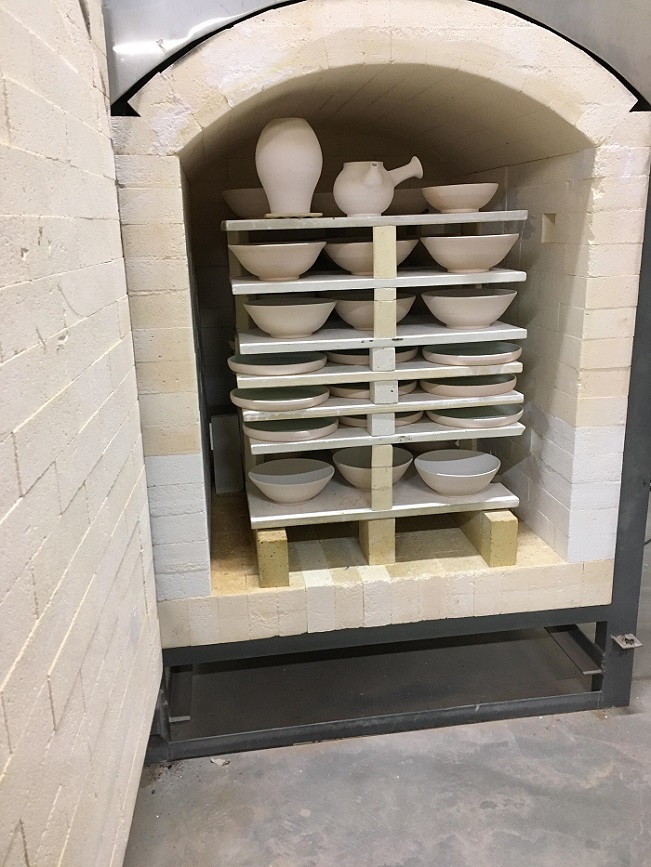
Wood-Fired
Perhaps the oldest and most traditional method of firing pottery is through a wood-fired kiln, which uses firewood as its fuel source. It’s usually made from bricks and lined with ceramic blankets for added protection during the firing process. When the heat is intense enough, the wood can combust and provide a much higher temperature than electric or gas-fired kilns.
The traditional nature of this method makes it the most unpredictable type of kiln and requires careful monitoring to ensure your ceramic piece doesn’t suffer from too much heat or smoke. If there’s too much smoke present, the glaze on your piece won’t be able to properly adhere and you’ll lose some of its aesthetic value.
Raku
This specialised type of pottery kiln is used to achieve a unique and beautiful finish that can’t be replicated by any other firing method. It’s designed to be easily portable and small enough to fit in a car. They’re heated using gas or wood and the temperature range is somewhere between 1000-1800°C, which results in a faster firing process than other types of kilns.
The end result is an incredibly unique glaze that’s unpredictable and lustrous. The intricate designs that are produced with this method are a testament to the skill and craftsmanship of any dedicated ceramist.
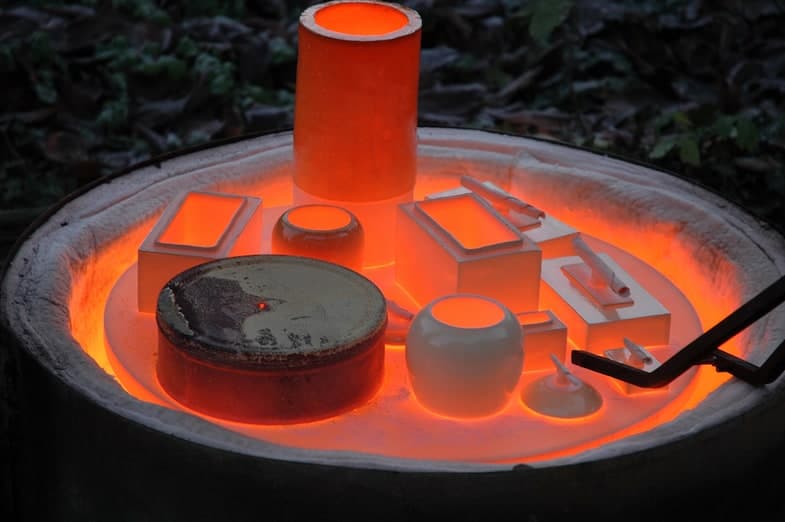
Main Considerations in the Firing Process
Even if you’ve got a seemingly appropriate kiln for your piece, you still need to consider a few key factors that come into play during the firing process. Oftentimes, there’s more to it than meets the eye, so understanding the different variables will help you in your quest for the perfect ceramic piece.
Size and Shape
This depends on what kind of item you’re trying to create, as different sizes and shapes require more or less heat in order to fire properly. If your kiln is too small for your ceramic piece, it won’t be able to handle the amount of heat and pressure required for the firing process. On the other hand, if it’s too large, then you’ll be wasting an unnecessary amount of energy.
Additionally, if your piece has any intricate details or asymmetrical shapes, you’ll need to make sure the kiln is capable of reaching those areas without suffering from heat loss. When you take the size and shape of your item into account, you’ll be able to determine the right kind of kiln for your ceramic masterpiece.
Temperature Controls
When you have control over the temperature, you can adjust it accordingly to make sure your piece is fired just right. Electric and gas-fired kilns allow for precise digital temperature control, whereas wood-fired and raku kilns are typically left to the discretion of the ceramist.
Depending on what you’re trying to create and how you want it to look, you’ll need to determine the right temperature for your kiln. Too low of a temperature won’t be enough to fire your piece, while too high may cause it to crack or break when exposed to the heat.
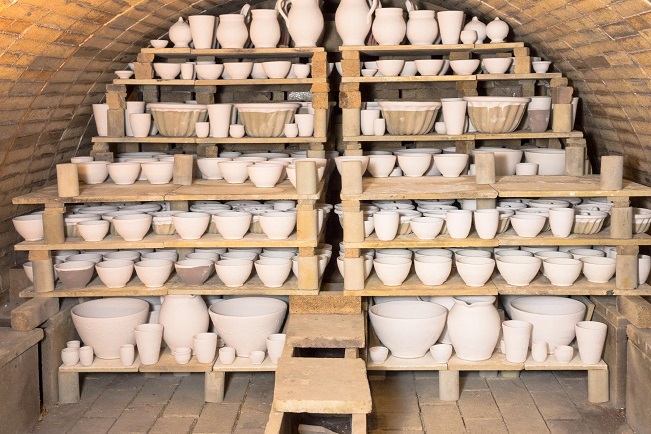
Firing Speed
This refers to how quickly the temperature rises and falls during the firing process. You’ll need to take into account how long it takes for your kiln to reach a certain temperature and also how quickly it cools down afterwards.
In general, electric and gas-fired models are faster than wood-fired and raku versions, as they reach higher temperatures in a shorter amount of time. However, faster firing speeds may not always be suitable for your piece, as the glaze may not be able to adhere properly in certain cases.
Ventilation System
In an extremely hot environment like a pottery kiln, proper ventilation is absolutely essential. It helps to regulate the temperature and remove any fumes that could otherwise be hazardous to your health. Whenever there’s smoke present, it needs to be directed away from the area so it doesn’t interfere with the firing process.
Electric and gas-fired models usually come equipped with a ventilation system that helps to keep the air clean and clear. It takes some of the heat away from the kiln and pushes it outdoors, allowing you to work in a safe environment. Other types, such as wood-fired and raku kilns, require the installation of an external ventilation system.