If you’ve modified or tuned your car, you’ll know that added power comes at a cost. Modded engines produce immense heat, and preventing that heat from radiating to other engine and vehicle parts limits wear and reduces damage. To this end, tuners use automotive heat wrap. This wrap lines the exhaust tubing and combines other heat insulation products in the engine bay and car underbody for multiple benefits, including improved engine efficiency and increased power.
Basics of Heat Wrap
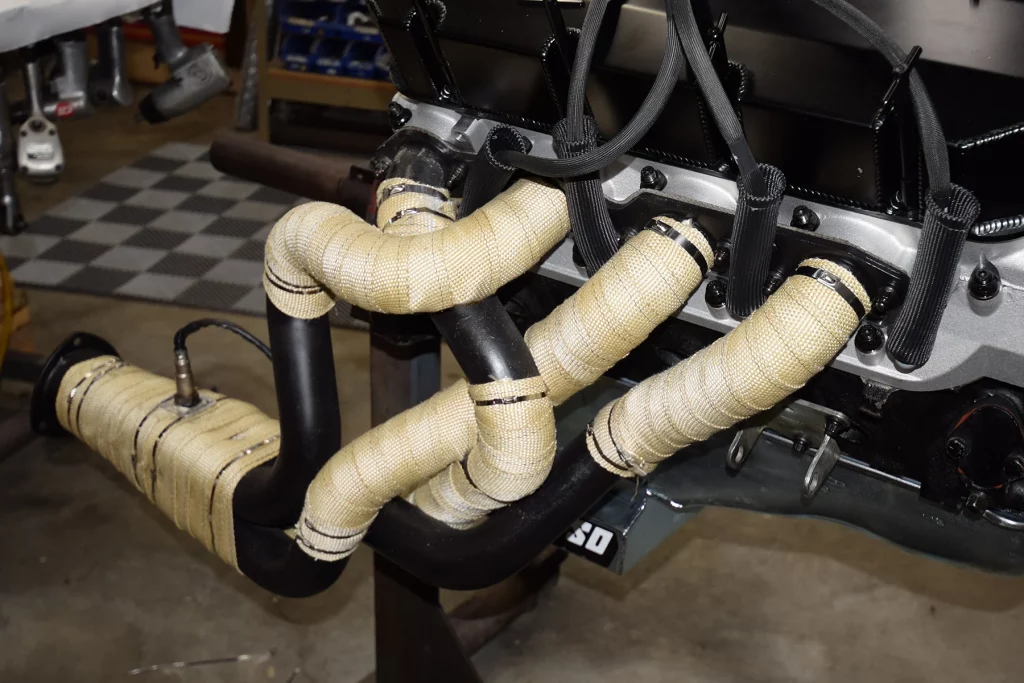
Exhaust heat wrap goes by a few other names, depending on where it’s used. This can contain high temperatures in the headers (header wrap) or, more commonly further down the exhaust piping (exhaust wrap). As a specialist material derived directly from the race track, exhaust wrap protects the car’s exhaust and manages heat inside the tubing.
By limiting the heat of exhaust gases inside the tubing, the protective heat wrap does a few things for your car. Hotter, spent gases exit the car faster, so they help with airflow and scavenging, basically allowing the engine to breathe. Moreover, with the wrap applied to the headers, the intake can draw cooler and oxygen-rich air, the basic ingredient for more power.
Consider the Long List of Benefits
Wrap may be simple and unassuming, but has many benefits:
- Improved heat management – high temperatures can cause significant damage to numerous car components, including the engine, rubber hoses, plastics, paintwork and the wiring. Using heat wrap reduces radiant heat and minimises the risk of heat damage, particularly in stock performance and tuned cars.
- More power and torque – keeping heat within the exhaust increases engine efficiency and power. Exhaust wrap adds a performance boost by improving exhaust flow and reducing air intake temperatures. Cars with turbos see significant power gains with higher volumes of cooler air.
- Reduced engine bay temperatures – exhaust wrap significantly reduces temperatures in the engine bay, leading to more tolerable heat levels inside the cabin.
- Lower fuel use – header wrap helps maintain consistent air density, which directly impacts performance and fuel consumption. By keeping heat in the exhaust, your engine will also be more efficient and consume less fuel.
- Improved sound insulation – exhaust wrap cuts down exhaust noise for a more refined driving experience.
- Aesthetics – the material also looks good, regardless of whether it is used on header pipes on classic cars or to hide heat stains and road damage in motorcycle exhausts.
Main Types
Header wraps are made of two basic materials: fibreglass and titanium. Fibreglass variants are good general-purpose wraps, often used to limit heat in stock cars. They can withstand temperatures up to 500 degrees, but they need to be wetted before applying and require a silicone coating to prevent leaks.
For performance and tuning applications, choose titanium wrap. This consists of crushed basalt rock, which is then woven into a fibre. The material has a much higher heat ceiling of 1200 degrees, making it more suitable for turbocharged engines with high heat cycling. Titanium heat wrap is pliable, doesn’t require wetting, has better uniformity and is easier and faster to install. Moreover, it’s resistant to oil and is non-toxic and recyclable.
Choosing Exhaust Wrap for Your Needs
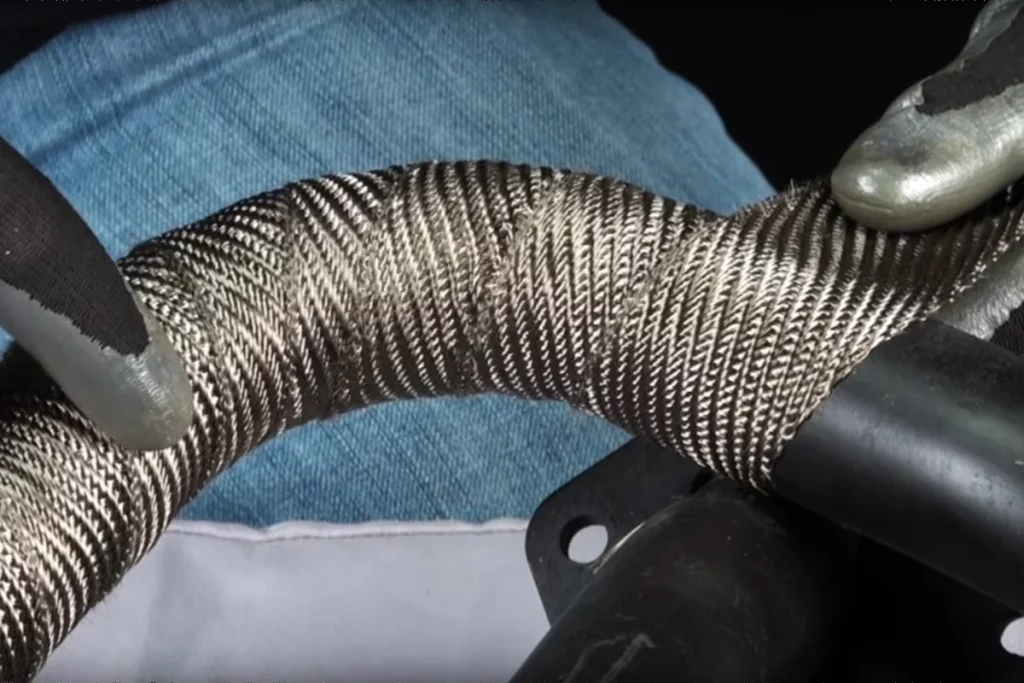
To purchase the right exhaust wrap for your vehicle, consider temperature requirements, overall durability, simple installation and aesthetics. Manufacturers state figures as either continuous or intermittent heat levels, that is, the highest temperature at which the exhaust wrap works optimally and the highest possible temperature until it ignites and burns up.
Titanium wraps have a continuous temperature rating of 1200 degrees but can also endure spikes of 1800 degrees for several seconds without igniting. This makes them the ideal heat insulation wrap for exhaust and turbo manifolds, downpipes and catalytic converters, as an illustration turbo manifolds often reach 950 Celsius.
Exhaust heat wrap also needs to contend with oil, coolant, gassing batteries and other chemicals and still perform. Titanium wraps, in this regard, far outlast fibreglass types without costing that much more. They’re also more flexible, easily adhere to the contours of exhaust piping, and, when applied with supplied cable ties, maintain a firm hold.
Aesthetics also play a part. Fibreglass wraps come in black, white and tan, while titanium is black or gold. If you’re doing extensive heat insulation with rigid heat shields and tapes, ensure matching colours for a neater look.
Lengths, Widths and Installation Tips
Choose 25 mm wrap for narrower straight and mid-pipes and 50 mm wrap for tubing between 45 and 100 mm or parts like headers and downpipes. Both types are sold in 15-metre rolls. To ensure a clean and tight fit, clean the exhaust of oil, dirt and other contaminants before applying the wrap.
Leave the sewn edges exposed and overlap the adjacent edges, aiming for a 25 per cent overlap. Use hose clamps to ensure the tightest possible fit. Once you’re done, the wrap is tightened in place with cable ties and excess cable removed. Conceal cut ends for a clean look and to prevent fraying.