While it’s not unusual for people who don’t weld to lump all the different types of welding activities into the same category, brazing is unlike any other hot metal joining process. Instead of relying strictly on heat to fuse an alloy filler with the base metals to create a joint, brazing relies exclusively on the melted filler’s capillary action to form joints. The base metals themselves aren’t melted during the brazing process, and it’s this seemingly unimportant difference that allows it to enjoy a host of advantages that other high-temperature joining processes lack.
Ideally, because brazing only requires the filler to melt, professional fabricators and welders are able to avoid a range of complex chemical, and situational considerations that could arise if they needed to join dissimilar metals. That’s why low-cost brazing is the professional’s preferred joining method whenever possible, as well as for beginners who are just getting acquainted with the joys of metal joining
LPG Brazing Takes the Worry Out of Metal Joining
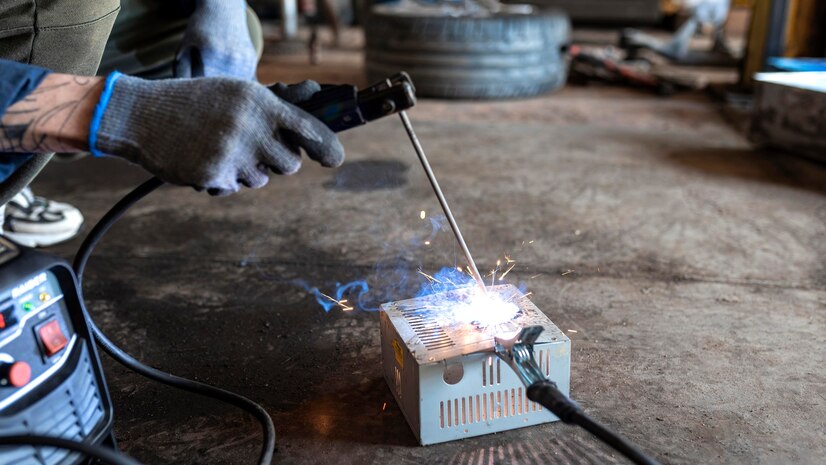
No matter if you’re a licensed professional pipe fitter, or a hobbyist who’s interested in fabricating panels for a classic car in your garage, learning to comfortably use an LPG torch and brazing rods is one of the most effective metal joining skills you can learn. Brazing allows you to join almost any ferrous, non-ferrous, or cermat (ceramic and metallic) composite, making it arguably the most flexible form of metal joining there is.
Although it’s largely accepted that brazed connections aren’t as strong as wire welded MIG and TIG joints, brazing still offers sufficient non-structural strength for all but the severest applications: a characteristic that’s underlined by the type of fuel that’s used. Brazing can be performed with a full range of fuels, including oxy/acetylene and MAPP gas, but the 425°C – 1200°C flame temperatures used primarily with low-cost LPG brazing torches are utterly tame when compared to the 3300°C welding electrode, and 19,000°C process temperatures used in acetylene welding.
The fact that brazing processes don’t reach temperatures that would liquify the base metals is the most critical aspect of its flexibility, and these lower fusing temperatures offer a generous array of joining benefits, including:
- No problems with joining dissimilar base metals;
- A higher calorific value with lower processing temperatures;
- Reduced chance of warping, or altering base metal chemistry;
- Decreased likelihood of a secondary fire hazard; and,
- Neater, cleaner joints that require less cleanup.
What brazed joints inherently lack in the tensile strength of their welding wire equivalents, they make up for in penetration. The flow-through capilary action of brazing alloys allows you to form lap, and socket joints that are just as strong as any made with high-temp welding wires, but without the risk of weakening, or burning through the base metal.
Brazing Rods Formulations for Every Metal
While brazing’s less aggressive behaviour toward base metals is due to its low heat requirements, its ability to join so many metals, especially dissimilar ones, is due to the wide range of brazing rod formulations. Differences in metallurgy, thermal expansion and melting rates, and galvanic composition make it impossible to use regular welding rods to just “melt and mix” so many metals together; this is where the eutectic properties of metal brazing rods become so important.
With or without flux coating, modern brazing rods offer some of the most complex alloy formulations in metal fabrication, and they’re available in a wide range of compositions that include:
- Nickel bronze. With its 935°C melting point, nickel bronze brazing rods provide maximum bonding strength and hardness for high-temperature resistant nickel, and nickel- and cobalt-based alloys.
- Tobin bronze. Tobin’s 890°C melting point, and excellent wear and corrosion resistance make it an ideal joiner for low-stress brass, bronze, copper, and copper alloy applications.
- 2% – 56% Silver. Silver rods feature an 800°C melting point, are known for their excellent flow qualities, and are used extensively for copper tubing on heating and cooling systems, plumbing, and hot water tanks.
- Manganese bronze. High-strength, self-fluxing manganese bronze metal brazing rods feature a melting point of 900°C, and are good for steel, stainless steel, or cast or malleable iron, even when galvanized or rusty.
- Aluminium. With a melting point of 380°C, aluminium brazing rod boasts a silicon content of less than 5%, and is used to braze aluminium, aluminium cast alloys, brass, copper, and bronze.
Make no mistake: while MIG and TIG welding are perfect for similar base metals, relying on their extreme heat to join dissimilar metals is an undertaking that’s rife with problems. Everything from cracking and warping due to differences in rates of cooling, to galvanic corrosion and oxygen reactivity can occur when melting incompatible metals together. The wettable action of brazing eliminates those problems and can achieve amazing results when done properly.
Top Tips for the Most Reliable Brazing Joints
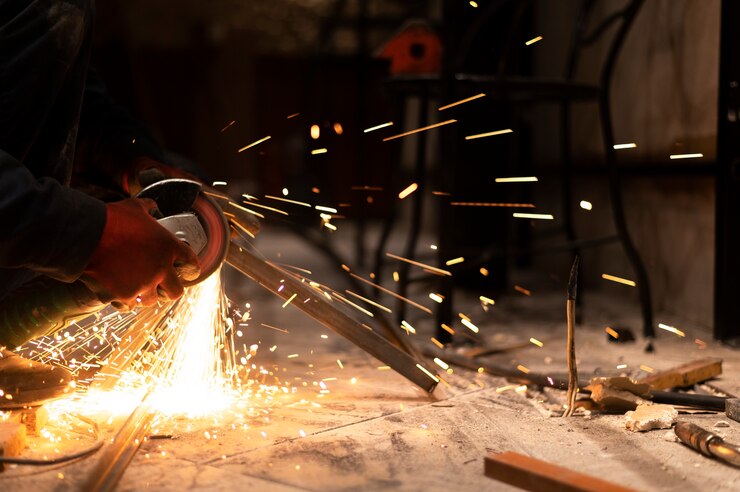
Unlike MIG and TIG welding processes that can take years to become reasonably capable, brazing is a relatively easy and economical process to master. Starting with a fabricator’s first attempt, it doesn’t require a lengthy learning curve, time-consuming machine setups, or need a continuous power source to achieve professional quality results.
In spite of the process’s simplicity though, there are a few basic rules that have to be followed for a brazed joint to be successful.
- As much as possible, thoroughly remove all dirt and grease from areas where the brazing filler needs to flow.
- Compensating for thermal expansion, ensures the base metals are clamped into position and unable to move.
- Ensure there’s sufficient clearance between the base metals to allow for adequate filler flow through.
- Be sure to apply heat evenly to the base metals before introducing the brazing rod.
- If the brazing rods aren’t flux-coated, don’t forget to apply flux before using the rod.
- Once introduced, continue to sweep the torch over the base metals to promote maximum filling of the joint.
- Don’t forget to clean away any residual flux once the joint is filled.
You also want to avoid using too much filler, as it can lead to heat and material buildups that can compromise the reliability of the joint.
The Final Word
At the end of the day, while MIG and TIG welding provide some of the strongest joints possible for the widest range of on-the-spot fusing applications, brazing offers the low-heat alternative that allows fabricators to work in close confines and with dissimilar metals. Depending on the type of joint, it can still be counted on to be just as strong as any that could be made with higher heat.
Everything depends on the fusing material that you’re using though, which is why you want to invest in the highest quality LPG torches, and the broadest selection of brazing rods available. There’s no substitute for employing the best alloys for the job, and it’ll be reflected in the reliability of your joints.