Among many other decisions Australians need to make during construction projects, they also must consider the best way to protect their homes against water damage. In contemporary construction, waterproofing membranes are crucial elements that act as protective barriers to prevent water from entering building structures.
These unique materials are essential for preserving the structural integrity of buildings, avoiding water destruction, and prolonging the lifespan of construction projects. The selection and proper installation are integral to creating watertight building envelopes helping to keep out moisture-related issues.
What Is a Waterproofing Membrane?
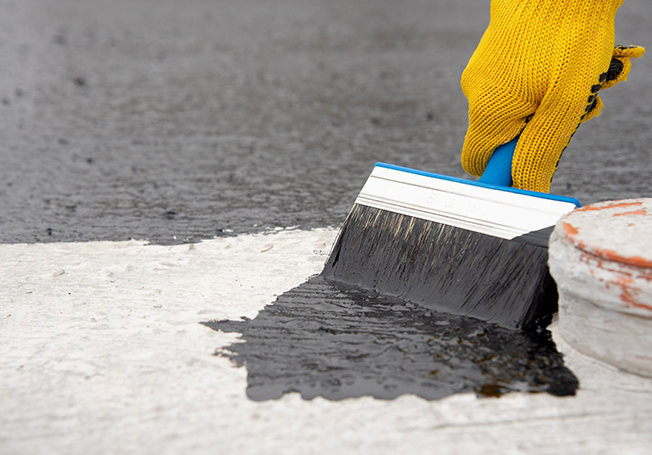
A waterproofing membrane is a continuous layer of water-tight material that stops water from penetrating from one area to another. These membranes effectively prevent both liquid water and water vapour from penetrating the elements of a building. The performance of waterproofing membranes is influenced by its constituent material, how it’s installed, and its compatibility with the base surface it’s applied to.
Different Types of Waterproofing Systems
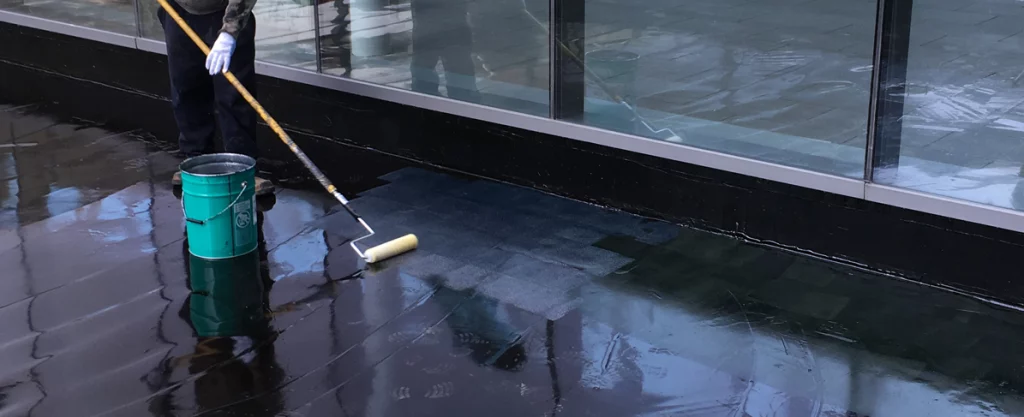
Sheet Membranes
Sheet membranes are pre-made materials available in rolls. These are modified bitumen, thermoplastic membranes such as PVC and TPO, and EPDM rubber membranes. Because sheet membranes are manufactured and available in fixed sheets, they provide consistent thickness and reliable quality over different applications, especially in larger areas. This is especially relevant in roofing and below-grade waterproofing applications where uniform coverage is critical.
Liquid Applied Membranes
These are fluid materials that cure to form a continuous waterproofing membrane. The products mainly include polyurethane-based material, acrylic and bituminous-based products among others. Liquid membranes are excellent for irregular surfaces, and complex geometries, thus providing a perfect fit for details and penetrations. They are widely used in wet areas such as bathrooms and balconies with multiple penetrations and complex details.
Torch-on Membranes
Torch-on membranes are bitumen sheets that have been treated and heat-welded to the substrate using a gas torch. These membranes are robust and are often used in commercial roofing applications. The installation of these solutions requires skilled professionals who know how to work with open flame and apply proper heat.
Applications in Construction
To prevent water damage to adjacent spaces, furniture, and structures, water areas must be carefully waterproofed. Australian standards outline specific requirements regarding wet area waterproofing, such as minimum upturn heights and penetration treatment. In these cases, professionals rely on liquid membranes, which can create uninterrupted barriers around fixtures and drain points.
Basement and below-grade applications require consistent and durable waterproofing systems to withstand hydrostatic pressure and damp soil. Sheet membranes such as those commonly made with modified bitumen and PVC products are common in these applications due to their high puncture resistance and crack-bridging capabilities between the substrate and overlay.
One of the most important applications for waterproofing membranes is in roofing. Sheet and liquid membranes are both used for roof coverings, depending on the roof design, climate conditions, and accessibility requirements. Specialized root-resistant membranes are commonly used for green roofs to maintain the integrity of the property under the foliage.
Balconies and podium decks that may be exposed to weather conditions and foot traffic present a unique challenge. These regions require a foundation waterproofing membrane that is resistant to both ecological and mechanical stress. A waterproofing system with a protective overlay is oftentimes used to provide a long-lasting performance.
Compliance and Standards in Australia
The Australian Standards that govern external waterproofing membranes are AS 4654.1-2012 and AS 4654.2-2012. They detail requirements for materials and installation practices used in external above-ground applications. They offer critical guidance on membrane selection, installation procedures, and testing requirements.
AS 3740-2021 relates specifically to waterproofing of internal wet areas in domestic premises. This guide provides the necessary waterproofing requirements for wet area configurations, ensuring minimum performance requirements of waterproofing systems.
- Among the key compliance requirements are:
- Specifications for minimum membrane thickness
- Requirements for tensile strength and elongation
- Resistance to UV exposure for exposed applications
- Water absorption limits
- The bond strength to common construction substrates
Establishment Responsibility and Quality Assurance
The performance of waterproofing systems is heavily reliant on their installation. Any certified installer must adhere to the manufacturer’s specifications as well as the relevant Australian standard. Measures for quality control include:
- Preparation of the substrates and checking their humidity
- Use of the proper primers
- Ensured membrane thickness as per specification
- Appropriate treatment to joints, corners, penetrations
- Flood testing where appropriate
- Installation guidelines and their documentation
Maintenance and Durability
Waterproofing membranes are typically long-lasting, with most examples providing a service life of several decades, but their longevity is very much dependent on maintenance and protection from damage. Regular inspections, especially regarding exposed membranes will allow issues to be detected before they result in water ingress. Most good waterproofing systems will provide effective waterproofing for 15-25 years when properly installed and maintained, however, service life is highly dependent on exposure and use patterns.
Takeaway
To ensure maximum integrity of the building structure, it is essential to protect it from water leaks and damages. Waterproofing helps you stay ahead of any potential water issues. Choose a team of licenced waterproofing professionals that will perform the job according to standards and provide you with the necessary documentation.