Hundreds of industries rely on compressed air as a power source. This is supplied by an air compressor to run different types of machinery, equipment and tools. Air compressors are used to power pneumatic tools such as impact wrenches, drills and nail guns, to inflate tyres and operate construction equipment, get water to farms, turn gas turbines, and package food and beverages. Compressors also work behind the scenes in hospitals, oil rigs, and manufacturing plants and even supply warm or cold air for your fridge and air conditioning.
The ubiquity of compressors is due to their high efficiency in converting electricity or fuel into usable power, their simple use, dependability and low maintenance needs, and the high levels of safety they provide. They also bring substantial cost savings, since matching air tools and equipment are much cheaper than conventional counterparts.
The Basics of Diesel Air Compressors
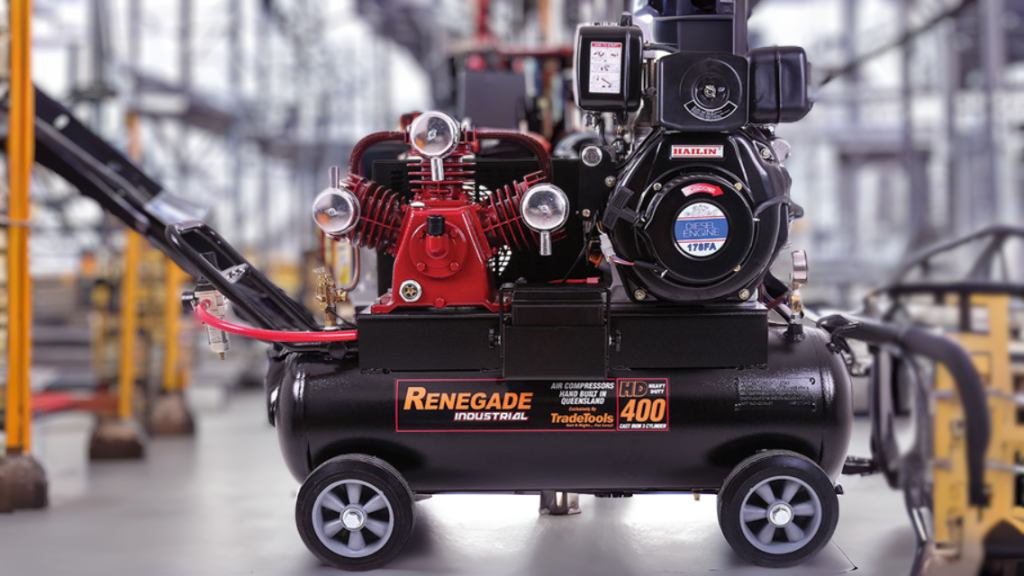
Compressors come in many shapes, sizes and types, but some of the most common are reciprocating diesel compressors. These consist of two basic parts, an engine running on diesel fuel and moving an air end or pump that does the actual compression. This happens as the engine turns a crankshaft acting on a connecting rod, cylinder and piston. The piston moves in an up-and-down (or ‘reciprocating’) motion within the cylinder. The downstroke creates a vacuum, drawing air into an inlet valve from the outside, which is then pressurised as the piston makes its way upwards. Once the piston reaches its peak, the air is compressed and exits through an outlet valve. The compressed air can be used as is, or stored for further use in tanks.
What Benefits Does a Diesel Compressor Bring?
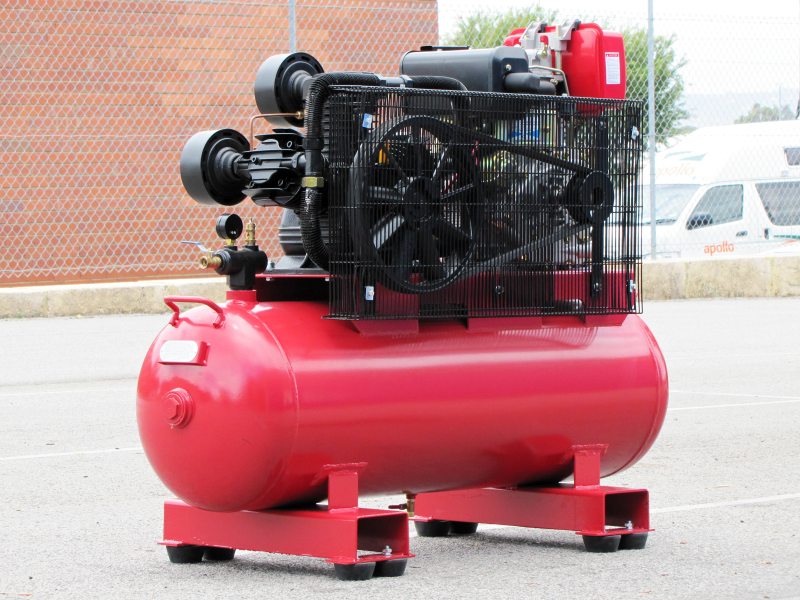
Compared to stationary compressors running on electricity and petrol variants that are generally higher maintenance and not primed for heavy-duty use, diesel compressors have a host of benefits:
- High power output – a diesel compressor can produce more power for the same displacement engine and piston count when compared to petrol variants. They’re also more suited to heavy-duty work with longer duty cycles and higher reliability.
- More efficient – Efficiency is one of the main reasons to go with compressors. Diesel is denser and produces more power, so for the same pressure and airflow to drive air tools like nail guns, you’ll soon be counting the savings. If you rely on compressors for more tools, then diesel is a reasonable choice.
- Robust build – this is another area where diesel-powered air compressors trump their petrol siblings. Parts are built to a better standard and have lower maintenance needs. They outlast both petrol and electric types in most applications.
- Quiet operation – combustion relies on compressing the fuel rather than igniting it, and this means lower decibels.
- Versatility – the ability to maintain high airflow and consistent pressure for longer puts diesel air compressors at an advantage. This widens the scope of tools and equipment that can be used, as well as how long they can operate at high torque. Look for additional features like water traps and regulators to remove moisture and provide cleansed air that won’t damage tools or equipment in the long run.
- Higher Safety – the industrial build, including cast-iron cylinders, included belt guards, and anti-vibration mounts means the compressor can be used in multiple settings without issue. Unlike electric variants, there are no risks of power outages or straddling cables.
- Portability – Smaller units are wheeled, so are easy to move where needed, whereas industrial-grade compressors pushing out 6 to 10hp have included fork pockets and can be easily moved with a forklift. For remote locations, like construction sites or farms, this is another key advantage over fixed electric compressors.
What to Look for in Your Next Diesel Compressor
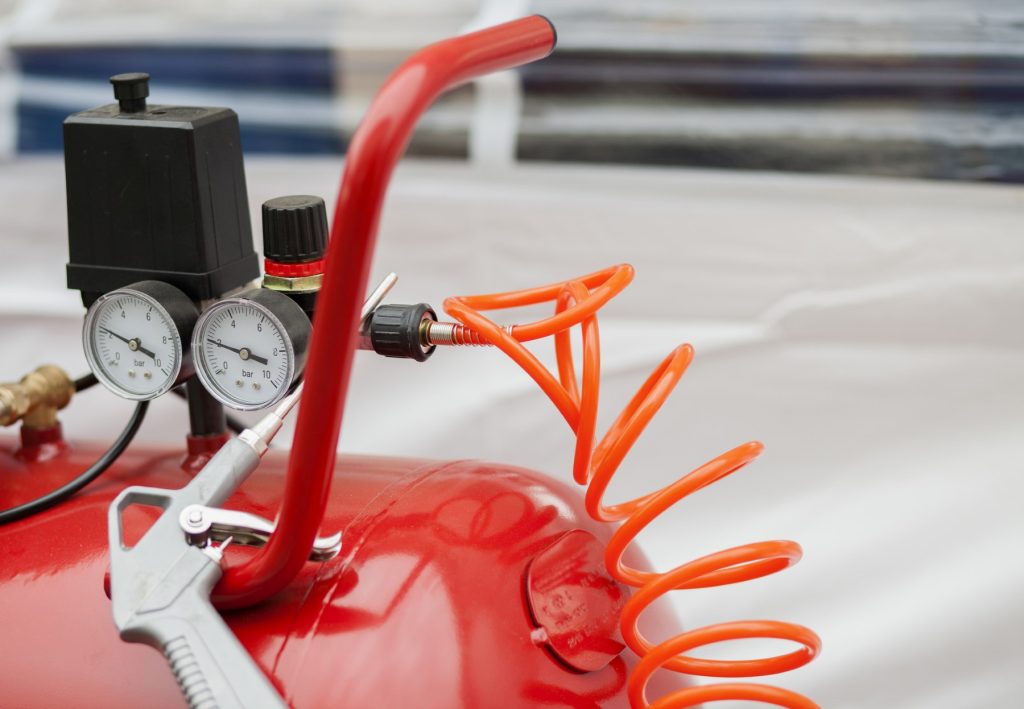
Airflow, air pressure, tank capacity, duty cycles and power output are the main factors when looking to buy diesel compressors. Airflow is measured in litres per minute (LPM). Industrial-grade compressors can put out over 400LPM at an industry standard of 90PSI of air pressure and are capable of running even the most demanding tools, such as concrete compactors, jackhammers, and heavy-duty sandblasters. Of course, a more robust and bigger compressor can generate more pressure, over 125PSI, for limited periods, if you need additional power in demanding tasks.
Tank capacities, storing up to 100 litres of compressed air, allow tools and equipment to be used for longer periods with little or no downtime needed. This considerably speeds up work. And with more power on tap, and 100 per cent duty cycles (due to superior cooling systems), a beefier diesel compressor can work for hours on end. Pair this with the powerful diesel engine, and you have a cheap and reliable power source for all compatible tools.
Of course, there’s more to numbers. And there are different needs. While heavy-duty compressors are the centrepieces of many industries and workshops, able to effortlessly drive a variety of tools, not everyone needs all the usability and reliability bigger units offer. If you work out of a shed or a garage and use basic tools in weekend renovations and DIY projects, then a smaller diesel compressor should tick most boxes.